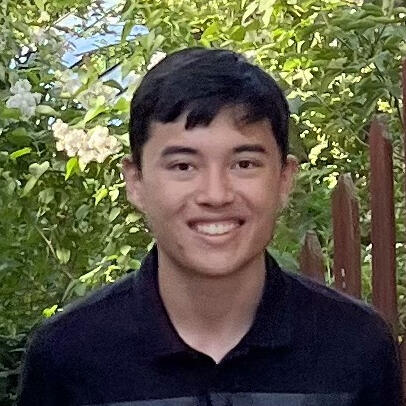
Robert Furuya
Engineer
Contact
Desktop plastic injection molder
As part of the yearlong Senior Design capstone at Trinity University, my team and I developed a desktop plastic injection molder for K-12 classroom use.An internal screw is turned using a hand crank to propel plastic pellets through the barrel. Shear force and heating bands combine to melt the plastic before entry into a mold mounted to the end of the barrel.We conducted extensive heat transfer, fluid mechanics, thermodynamics, gear ratio, mechanics of materials, and other analyses to inform the design of the molder. We also researched empirical correlations and methods native to injection molding.In the future, the device will be integrated into STEM curriculum developed in partnership with education students and professors at Trinity University.
Rover
In Summer 2023, I had the opportunity to contribute to a long-running autonomous rover project overseen by Dr. Kevin Nickels.The existing design was mostly functional, but very fragile. Wheels mounted to the rocker-bogie suspension experienced 30+ degree deflection under minimal load. I discovered that a lot of the torsion occurred at the steering column assemblies, so I redesigned the two front assemblies: reducing the number of parts and eliminating plastic and aluminum extrusion wherever possible. I designed a new belt-tightening system and new caps, and fabricated them out of solid aluminum using the Haas Mini Mill.The improvements greatly reduced the observable torsion. Similar strategies to streamline the assembly, eliminate weak joints, and use stronger materials were recommended for future development.
Music props and promotion
2019 and prior